Generalized plastic bottles are mainly used for liquid or solid disposable plastic packaging containers for beverages, food, pickles, cosmetics, agricultural and veterinary drugs, etc. Plastic bottles have the characteristics of being unbreakable, low cost, high transparency, and food-grade raw materials.
Introduction of plastic bottles for cosmetic packaging
1. The material of cosmetic plastic bottle is usually PP, PE, K material, AS, ABS, acrylic, PET, etc.
2. The cream bottle, bottle cap, bottle stopper, gasket, pump head and dust cover usually used for cosmetic containers with thick walls are injection molded; PET bottle blowing is two-step molding, tube blank is injection molding, and finished product packaging for blowing the bottle. Others, such as lotion bottles and washing bottles with thin container walls, are blowing bottles.
3. PET material is an environmentally friendly material with high barrier properties, light weight, non-breaking properties, chemical resistance, and strong transparency. It can be made into pearlescent, colored, magnetic white, and transparent. It is widely used in gel water. The bottle mouth is generally standard 16#, 18#, 22#, 24# diameter, which can be used with a pump head.
4. The acrylic material is an injection-molded bottle, which has poor chemical resistance. Generally, the paste cannot be directly loaded. It needs to be equipped with an inner tank to block it. , The packaging requirements are higher during transportation, because it looks particularly obvious after being scratched, has high permeability, and feels extra thick on the upper wall, but the price is quite expensive.
5. AS, ABS: The transparency of AS is better than that of ABS, and the toughness is better.
6. There are ordinary ink and UV ink for silk screen printing. UV ink has better effect, glossy and three-dimensional effect. During production, you should first make a plate to confirm the color. The screen printing effect of different materials will be different.
7. The processing technology of hot stamping and hot silver is different from that of printing gold powder and silver powder. Hard materials and smooth surfaces are more suitable for hot stamping and hot silver. It is better than printing gold and silver.
8. Bottle caps are generally equipped with inner gaskets, pull caps and inner plugs, and very few are equipped with spoons or droppers, which are mainly due to their tightness and convenience of use.
(1), cream bottle + outer cover (production machine: injection molding machine)
The PP and PETG materials that are often used in the injection cream bottle body (new materials, good transparency, no need to add inner liner, but there are also double layers, in order to save costs), acrylic (this product has good transparency, generally need to add inner liner, not directly Paste, the bottle body will crack), ABS material (the variety of this material is used for electroplating accessories, easy to color), the cover is mostly PP material, the inner cover is PP + outer cover acrylic or electroplating outer cover or anodized aluminum outer cover or fuel injection cover
Craftsmanship:
Bottle body: PP and ABS bottle body are mostly made of solid color, PETG material and acrylic bottle are mostly used transparent color, which has a translucent feeling, and acrylic bottle wall is mostly sprayed with color, which can reflect light and has good effect.
Printing: The bottle body can be screen-printed, hot-stamped and hot-silvered. The inner cover of the double-layer cover can be screen-printed, and the outer cover can be transparent. The outer cover is made of anodized aluminum and can be embossed with a logo.
(2), vacuum bottle + pump head cover (essence bottle, toner bottle, lotion bottle), injection molding vacuum bottle body commonly used AS material, can directly contact paste, no straw, vacuum design) + pump head (electroplating) cover ( transparent and solid color)
Production process: The transparent color of the vacuum bottle body is used more, and the solid color is used less.
Printing: The bottle body can be screen-printed, hot-stamped and hot-silvered.
(3), blowing
(Essence Bottle or Lotion Bottle, Toner Bottle) (Production Machine: Blow Molding Machine)
A. Understand the blowing process
According to the plastic material, it can be divided into PE bottle blowing (softer with more solid colors, one-time forming), PP bottle blowing (harder and more solid color, one-time forming), PET bottle blowing (good transparency, more useful for toners and hair products). , is an environmentally friendly material, formed twice), PETG blowing (brightness is better than PET, but not commonly used in China, high cost, high cost, one forming, non-recyclable materials) less.
Combination form: blowing bottle + inner plug (commonly used in PP and PE materials) + outer cover (commonly used in PP, ABS and acrylic, also electroplating, and anodized aluminum, most used in oil spray toner) or pump head cover (usually used in essence and lotion ), + Qianqiu cover + flip cover (lift cover and Qianqiu cover are mostly used by large circulation daily chemical lines).
B. Bottle blowing production process:
Bottle body: PP and PE material bottle body mostly use solid color, PETG, PET, PVC material mostly use transparent color, or colored transparency, with a sense of translucency, and use solid color less. PET material bottle body is also available with spray color.
Printing: silk screen and hot stamping, hot silver.
(4), pump head
1. The dispenser is divided into two types: tie type and screw type. In terms of function, it is divided into spray, foundation cream, lotion pump, aerosol valve, and vacuum bottle.
2. The size of the pump head is determined by the caliber of the matching bottle body. The size of the spray is 12.5mm-24mm, and the water output is 0.1ml/time-0.2ml/time. It is generally used in the packaging of perfume, gel water and other products. The length of the same nozzle can be determined according to the height of the bottle.
3. The specifications of the lotion pump range from 16ml to 38ml, and the water output is 0.28ml/time - 3.1ml/time. It is generally used for creams and washing products.
4. The vacuum bottle is usually cylindrical, with a specification of 15ml-50ml, some 100ml, and the overall capacity is small. It relies on the principle of atmospheric pressure to avoid pollution caused by cosmetics during use. The vacuum bottle has anodized aluminum, plastic electroplating and colored Plastic, the price is more expensive than other general containers, and the general order quantity requirements are not high.
5. PP materials are mostly used, (production machine: injection molding machine) outer ring is also made of anodized aluminum sleeve, and electroplating process is also used. It can also be gilded and silvered.
(1) According to the function of the bottle body:
A. The pump head of the vacuum bottle, without a straw, + cover. B. The pump head of the ordinary bottle needs a straw. + Cover or without cover.
(2), according to the function of the pump head
A. Lotion pump head (suitable for lotion-like contents, such as lotion, shower gel, shampoo). B. Spray pump head (suitable for water-based contents, such as spray, toner).
3. According to appearance
A. The pump head has a cover, and the cover plays a protective role. (preferably used for products with relatively small capacity) within 100ml. B. The pump head without cover has a special design, which can be locked, and the contents will not flow out due to squeezing, which plays a protective role and is easy to carry. cut costs. (Preference is given to products with comparative capacity.) Above 100ml, the pump heads of shower gels and shampoos on daily chemical lines are mostly designed without outer covers.
4. According to the production process:
A, electroplating pump head; B, anodized aluminum pump head; C, plastic pump head.
(5), outer cover
PP materials are mostly used, and PS, ABC materials and acrylic materials are also available. (Production machine: injection molding machine, divided into double-layer covers according to the structure:
A, PP inner cover + PS and acrylic material outer cover; B, PP inner cover + outer cover PP, ABS material electroplating; C, PP inner cover + anodized aluminum outer cover; D, PP inner cover + PP or ABS fuel injection outer cover cover.
Single layer cover: PP material is commonly used
Process: The edge of the cover can be gilded or silver, sprayed with oil
The inner cover of the double-layer cover can be screen-printed with a logo, and the outer cover is transparent to reveal the effect. The outer cover is made of anodized aluminum and can be embossed with a logo.
The main difference is that the materials are different. It is good that everyone can know the difference between these main materials.
PET: PET has high transparency, and the bottle body is soft, which can be pinched but harder than PP.
PP: PP bottles are softer than PET, easier to squeeze, and less transparent than PET, so some opaque shampoo bottles are more commonly used (easy to squeeze).
PE: The bottle body is basically opaque and not as smooth as PET.
Acrylics: Thick and hard, the most glass-like is acrylic.
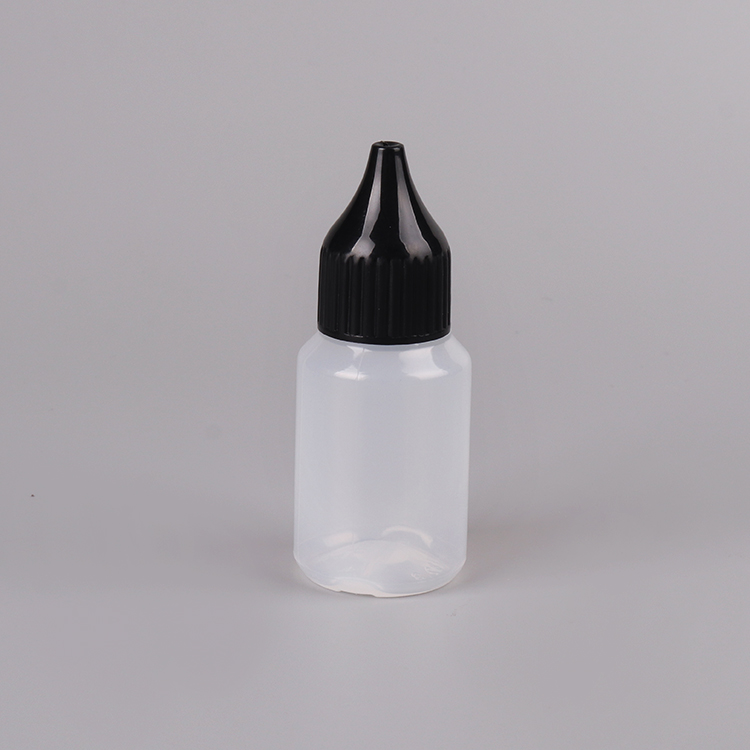